A toast to our teams!
Top performances at this year's certification
We are delighted to once again hold the well-deserved EFIT fashioncare “certified quality” and “certified hygiene” certificates in our hands. A milestone that underlines our efforts and demands for the highest standards and customer satisfaction.
Over the past year, we have invested a lot of time and effort in improving our quality. Be it through internal and external training or independent, unannounced inspections. Our efforts certainly paid off.
We are proud to announce that we have achieved 92/100 points at our locations in Wallisellen and Binningen and an impressive 94/100 points in Rotkreuz in this year’s certification. We would like to take this opportunity to thank our shop managers and their teams for their efforts. You are great!
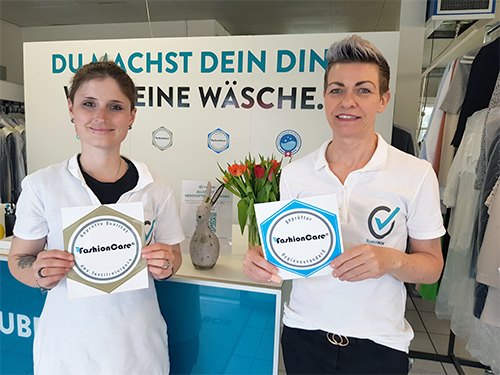
Team Rotkreuz
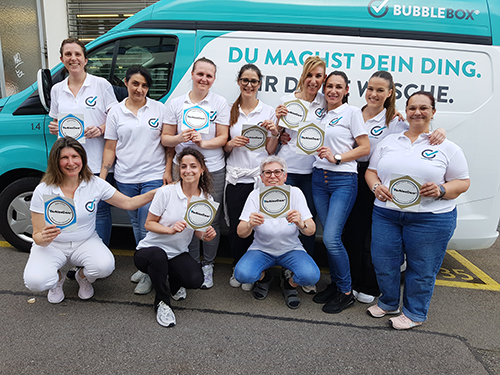
Team Wallisellen
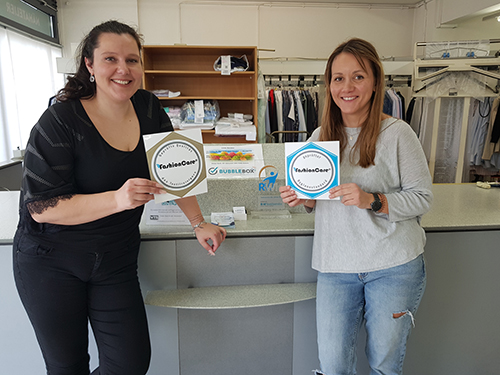
Team Binningen
What is EFIT Fashioncare " certified quality" and "certified hygiene" anyway?
The assessment is divided into two categories: Quality and Hygiene. In addition, individual training courses tailored to the location and requirements are carried out by EFIT managers as part of the quality assessment.
The following criteria are checked for quality:
- Workplaces: Are the workplaces neat and clean?
- Ventilation: Are the rooms well ventilated and do the outlets on the relevant machines work?
- Lighting: Is the lighting in the rooms and workstations sufficient (especially in the darker months of the year)?
- Machinery: Are the machines neat and clean, are they properly maintained and is maintenance carried out correctly at regular intervals?
- Stain removal: Are the stain removal detergents used correctly for the corresponding fabrics and stain type and, if stains cannot be removed, whether stain labels are attached to the goods?
- Ironing quality: Do the textiles have the necessary residual moisture to achieve a crease-free result? Are folds correctly positioned? Are the pockets, collars and cuffs ironed correctly? This is checked for both machine-ironed and hand-ironed textiles.
The following criteria are checked during the hygiene inspection:
- Washing programs: Are the various wash programs set correctly? Is the correct detergent and the correct amount added? Does the machine reach and maintain the water temperature as defined?
- Swabbing with Rodac plates: Swabs are taken of machines and equipment, transport containers and the finished textiles and the CFU (colony forming units) are checked, as the tolerance limit must not be exceeded.
Training:
On the day of certification, training is also provided by an EFIT representative. Some training topics are put together individually based on the needs of the company locations. However, there are also specific topics that are passed on to all participating companies.
These include, for example, technical innovations and textiles that are currently in fashion. Attention is drawn to what needs to be considered when caring for and cleaning them, where problems can arise and how the fabrics and textiles behave with the available types of treatment. For example, waxed jackets reappeared on the fashion horizon last winter. And as fashionable and classy as these jackets look, they tend to be a somewhat feared guest when it comes to textile care. When a waxed fabric is washed, the contact between water and wax causes it to break, just like a candle placed in water. If the waxed fabric is dry-cleaned, the wax dissolves due to the solvents. Either way, the result is probably not what customers want. However, the companies’ hands are tied, as none of the cleaning options lead to a satisfying result.
Furthermore, fashion-specific ironing trends are also part of the training. Depending on the fashion, strong creases are “in” or a more “round” ironing technique is required. General adjustments and possible difficulties in the industry are also addressed and solutions are worked out.
The exchange within the industry is very valuable for dry cleaning companies and we also value the support of EFIT enormously in this respect, as we can always learn from our competitors and pass on our knowledge.
At the end of the training, quality training is provided for specific workstations. Every step in the program is covered, from incoming goods to sorting the dirty laundry, loading and setting the machines to finishing and quality control.
The EFIT fashioncare certification of quality and hygiene is not only an award, but also proof of our commitment to quality, hygiene and cleanliness. We are delighted to have successfully passed this important inspection. Despite the excellent results, we will not rest on our laurels and will continue to perfect our quality and hygiene.